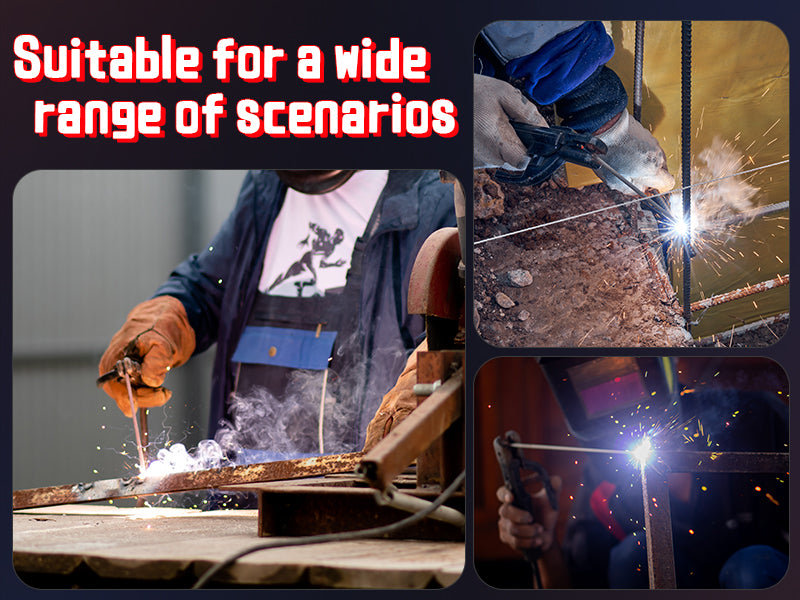
Welding PPE and Safety, Space Applications, and Metal Additive Manufacturing: Shaping the Future of Welding
The welding industry is evolving with groundbreaking advancements in safety measures, high-demand applications like space welding, and new technologies like metal additive manufacturing. These shifts are transforming traditional welding practices and introducing new opportunities and challenges across the field. Here, we explore the importance of welding PPE and safety, the demands of welding in space, and the rise of metal additive manufacturing.
Welding PPE and Safety: Protecting the Workforce
Safety remains a top priority in welding, where exposure to intense heat, fumes, and UV radiation makes PPE essential. The International Agency for Research on Cancer (IARC) identifies welding fumes and UV radiation as Group 1 carcinogens, underscoring the need for protective measures like fume extraction systems, respirators, and fire-resistant clothing
. Many companies have responded by developing advanced protective equipment that filters ultra-fine particles, enhancing the safety of welders in diverse environments. As health standards evolve, improved welding PPE is vital for reducing workplace hazards and ensuring welders' safety in various conditions, from enclosed spaces to outdoor job sites.
Welding for Space Applications: Meeting Extraterrestrial Demands
Welding for space applications brings unique challenges, including the need for equipment that can operate in microgravity and extreme temperature fluctuations. This specialized form of welding is critical for constructing space habitats, satellites, and other aerospace structures. Techniques like friction stir welding (FSW) and laser welding are favored for their precision and durability, which are essential for the rigors of space
. In addition, advancements in remote-controlled and robotic welding are enabling astronauts to perform complex welding tasks without direct exposure to hazardous conditions, paving the way for future space missions that involve on-site repairs and assembly of large structures.
Metal Additive Manufacturing in Welding: The Future of Fabrication
Metal additive manufacturing, or metal 3D printing, is transforming how parts are designed and fabricated in the welding industry. This technology builds components layer by layer, allowing for complex geometries and reducing material waste. Often used in sectors like aerospace, automotive, and medical device manufacturing, additive manufacturing enables faster prototyping, customization, and the production of intricate parts that traditional welding methods struggle to achieve
. With ongoing advancements, metal additive manufacturing is expected to complement traditional welding techniques, providing a versatile solution for creating high-strength, lightweight structures.
Conclusion
As welding technology advances, safety measures, space applications, and metal additive manufacturing are reshaping the industry. With improved PPE, innovative space welding techniques, and the integration of 3D metal printing, the welding profession is entering an era of unprecedented opportunities and responsibilities. These advancements not only promise safer and more efficient processes but also unlock potential applications that extend well beyond Earth.